Combined crack and grinding burn test with single sensor and array sensor on bearing rings and rolling elements
Non-contact, fast, high-resolution and efficient
In addition to a wide variety of tasks from industry, a current topic is crack and grinding burn testing on bearing rings and rolling elements. This customer requirement can be solved semi-automatically and also fully automatically. Depending on the test task, single probes or array probes can be used.
In the example shown, the inspection of rolling element components requires the detection of minute cracks and grinding burn. In order to meet the required cycle time in automated testing systems, array sensor technology is increasingly being used in these applications.
In the present case, an 8-fold sensor array is used for testing on the inner and outer ring. Six sensors are arranged in two staggered rows for testing the tread. For testing the side surfaces (rims), one sensor each is angled at 90°. The sensor array is controlled accordingly by the ELOTEST PL650 and the sensor elements required for the respective test are selected.
8-fold sensor array KDA-129 with six sensor elements arranged in two rows for testing the running surface of rolling bearing rings and two sensor elements arranged at 90° to each other for testing the thrust ribs.
Each sensor is a combined differential / absolute sensor. The absolute winding can be used both for electronic liftoff / distance compensation and (simultaneously) for additional testing for planar grinding burn.
The sensor array is connected to a test channel of the ELOTEST PL650 via a fast 8-fold multiplexer.
The ELOTEST PL650 is a digital eddy current tester and is ideally suited for all types of eddy current testing such as crack, heat treatment, (opens in new tab)material mix-up and grinding burn testing.
It has a connector for active sensor arrays with up to 64 sensors per channel. The high multiplex rate allows very high test speeds and thus significantly reduces the cycle time of the test and increases the throughput of the test system.
The ELOTEST PL650 with its array sensor technology is therefore ideally suited to implement fast and efficient crack and grinding burn testing in automated systems.
Source: Rohmann GmbH, internal application report.

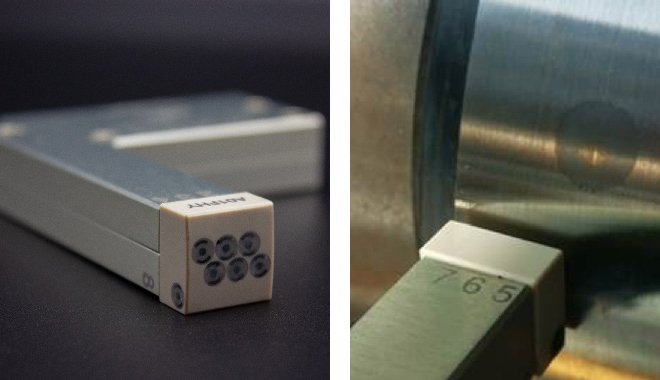
8-fach Sensorarray KDA-129 mit sechs in zwei Reihen angeordneten Sensorelementen zur Laufflächenprüfung an Wälzlagerringen und je zwei 90° hierzu angeordneten Sensorelementen zur Prüfung der Anlaufborde.


C-Scan-Darstellung einer Lauffläche mit zwei 1 mm Laserpunkten zur Simulation von Schleifbrand, gescannt mit den stirnseitigen Sensoren des Arrays. Darstellung und Verarbeitung im ScanAlyzer.